Warning
You are reading an old version of this documentation. If you want up-to-date information, please have a look at 5.2 .2.2 Results
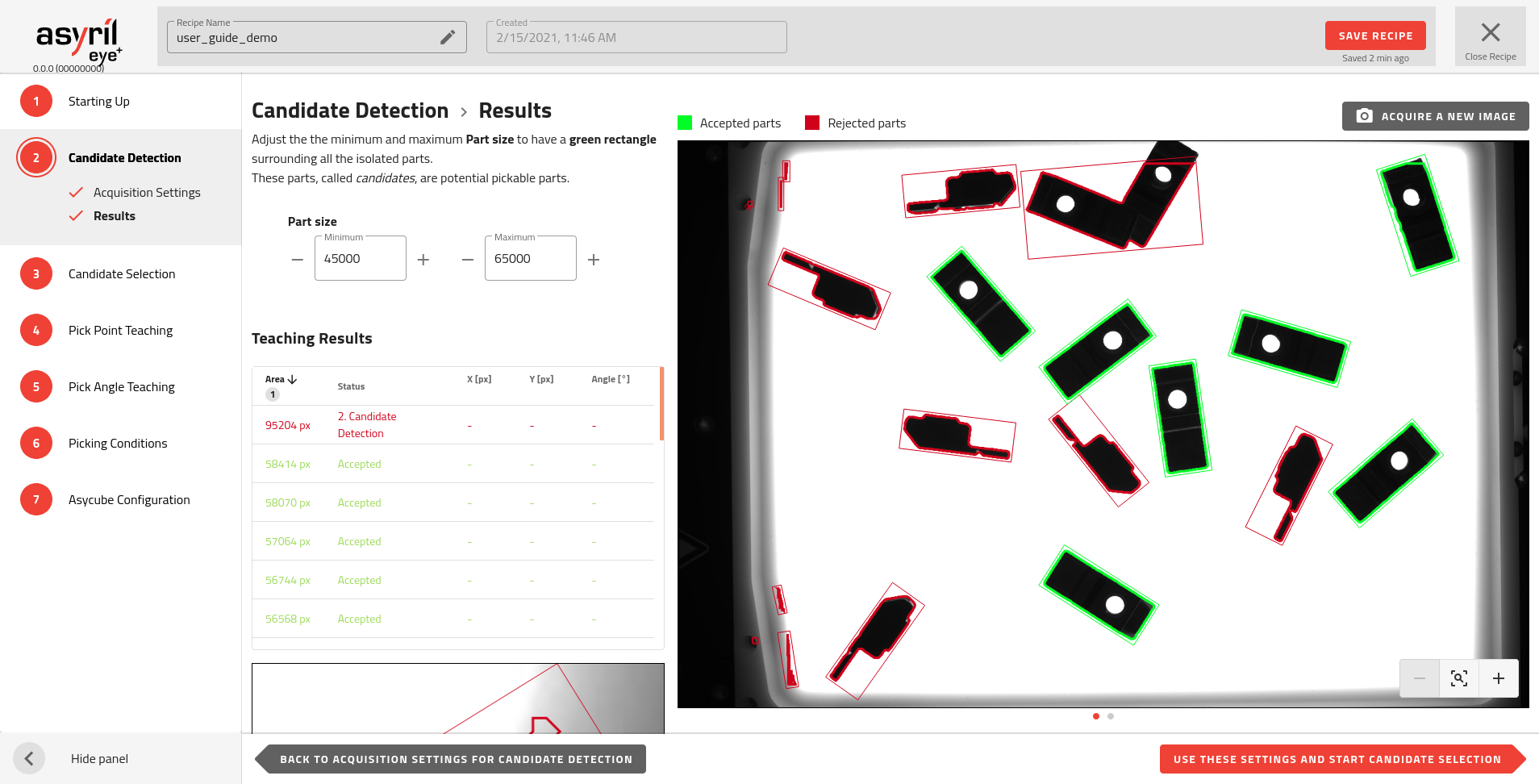
Fig. 70 Candidate Detection - Results
All contours detected by the algorithm can now be filtered depending on their area. You have to define which surface (i.e. part size) is considered as good by adjusting the minimum and maximum values. These values are either in calibrated unit or in pixels depending on the camera configuration. All contours within this range surface area will be considered as candidates for the next steps and the rest will be rejected.
Important
If a part is not surrounded by a green rectangle at the end of this step, it will be discarded for all the following steps, meaning that it will not be picked by the robot before a vibration is made to change its position or orientation.
Tip
You can manually move the parts on the feeder and then hit the “Acquire a new image” button to analyze a new picture and check if the candidate detection is performing well.
Note
If the part is a bit outside the Region of Interest (ROI), the detected borders of the part are cut as shown in Fig. 71. The bounding boxes may have a different size because of this. This part can still be used for the next steps but you should be aware that from the system point of view, the part is cut on the side.
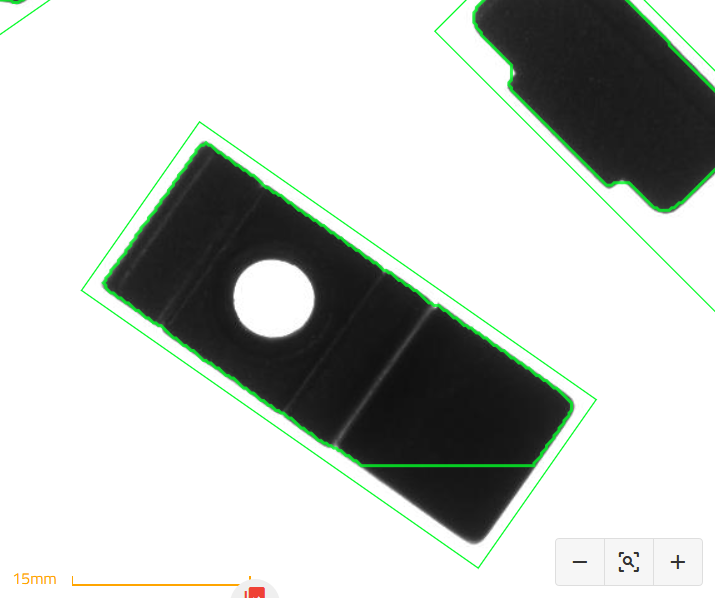
Fig. 71 The part is cut because it is a bit outside the ROI
Part size is too low or too high
Too low: Risk of detecting small dirt or shadows.
Too high: Risk of detecting a group of parts as a single part.
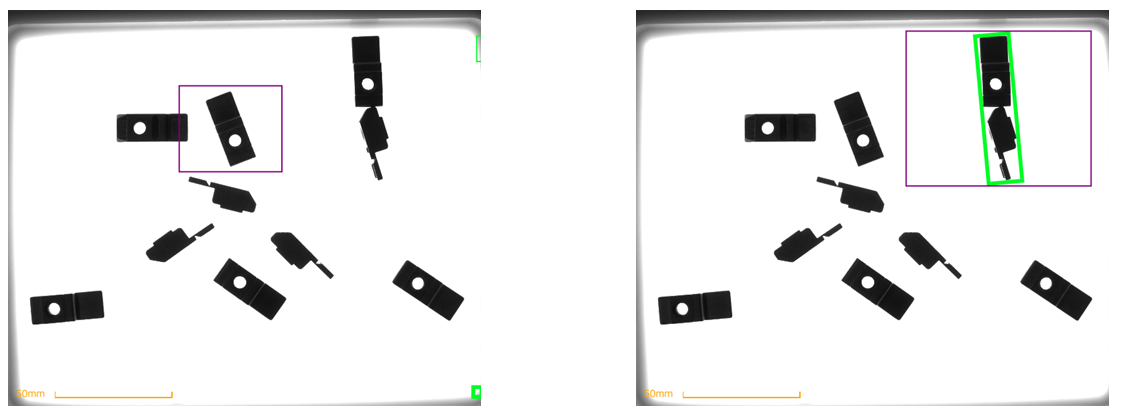
Fig. 72 Part size: too low (left), too high (right) [Backlight - 13ms]
Part size range is too narrow or too wide
Too narrow: Part detection may not be robust enough to detect a part in different positions in the image (slight change in the surface of the part seen by the camera). The risk is to reject a part only because its surface is slightly out of the desired range.
Too wide: Risk of detecting too many different part sizes and detecting groups of parts as a single part.
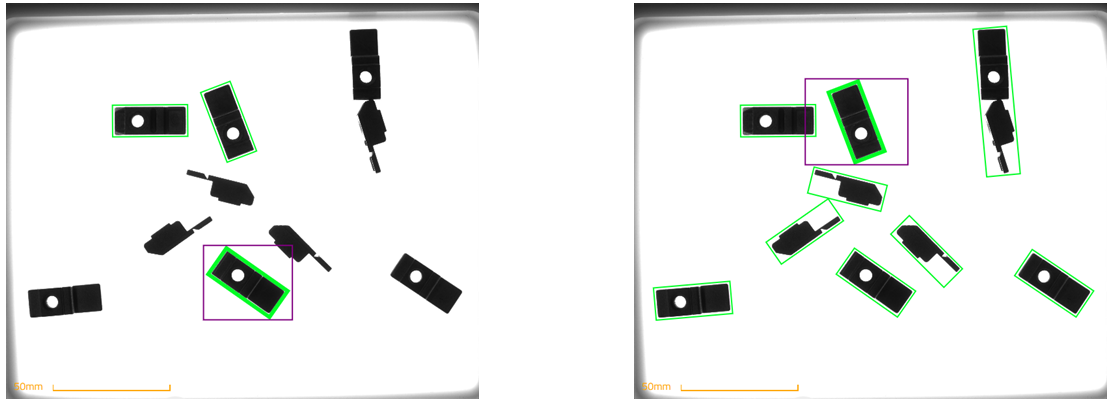
Fig. 73 Part size range is too narrow (left) or too wide (right) [Backlight - 13ms]